PP, PE film and PP woven bags recycling system china plastic washing machine
Product video:
PP, PE film and PP woven bags recycling system
Layout:
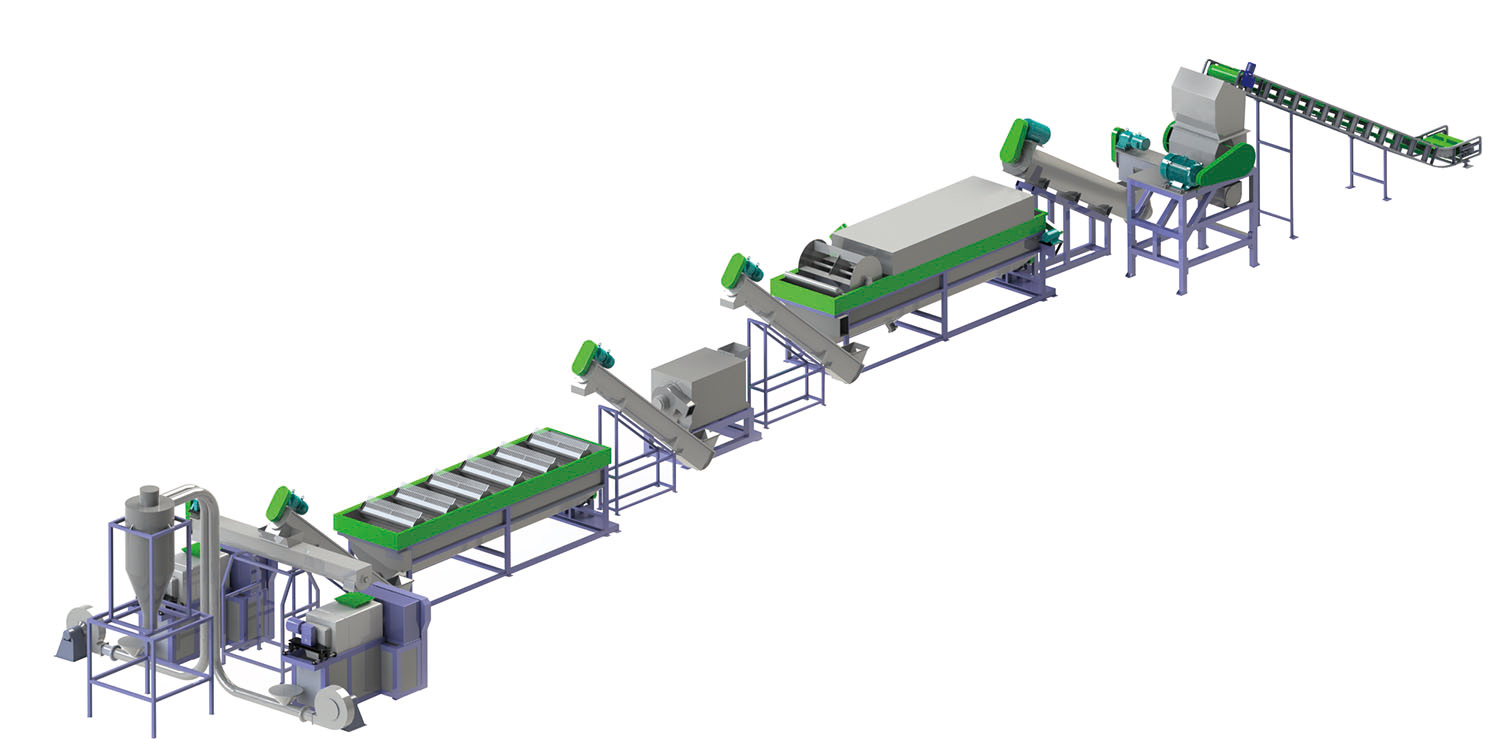
1.Belt conveyer
2.Crusher
3.Horizontal friction washing
4.High speed friction washing
5.Floating tank
6.Screw loader
7.Dewatering maching
8.Screw loader
9.Floating washer
10.Screw loader
11.Plastic squeezer dryer
The main washing machines features:
A.Horizontal Friction Washing
It is designed to effectively remove the sand and label stick on the films. Will add water to wash.
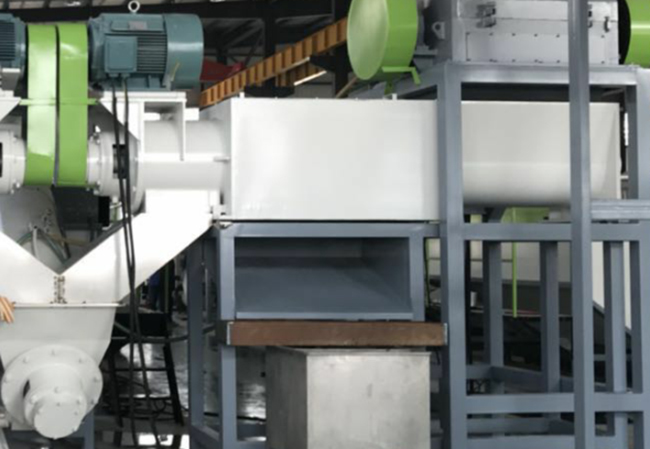
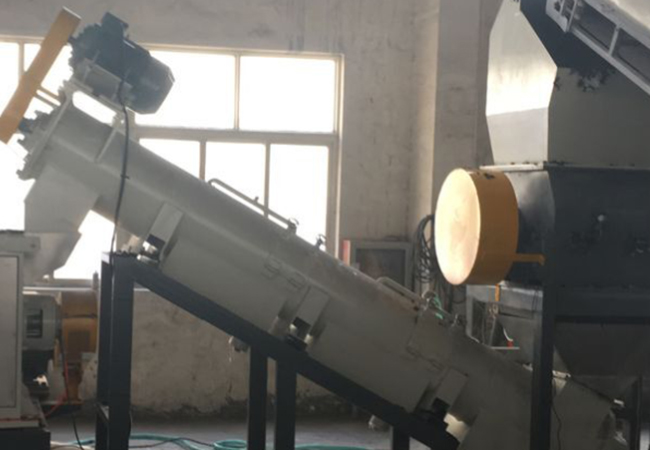
B.High speed friction washing
It is designed to remove the sand the labels stick on the films. Will add water to wash.(picture)
C.Floating tank
It will float the raw material. And according to raw material situation, we may add the pneumatic valve to discharge the waste and sand. The design of the stainless steel chain to discharge waste to save the water.(picture)
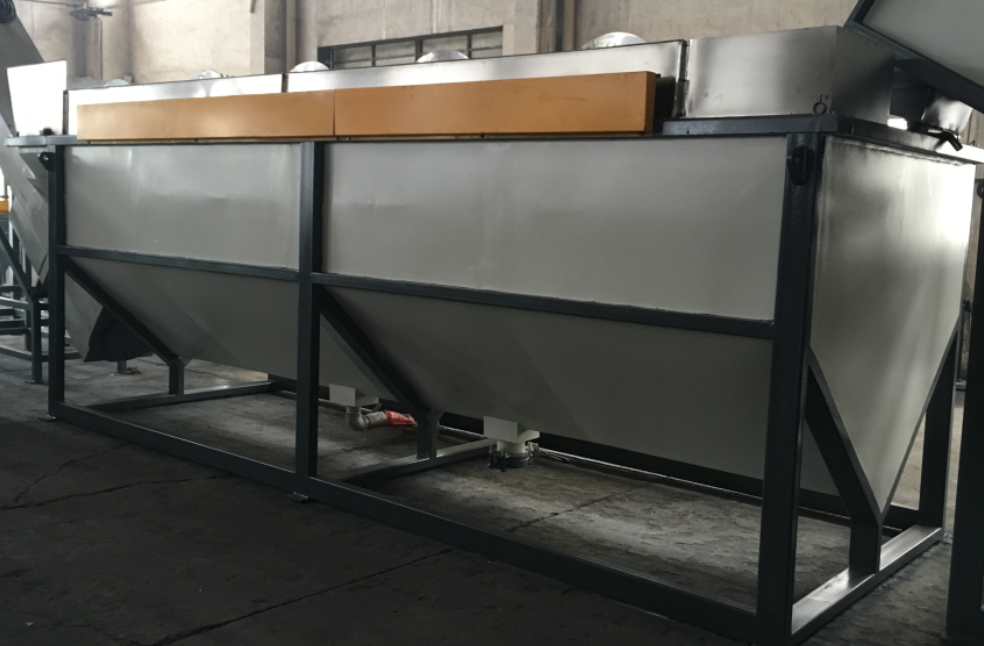
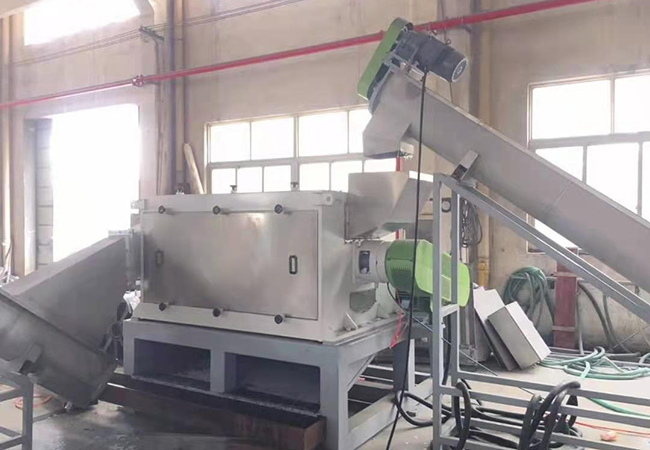
D.Plastic dewatering machine
The dewatering machine removes dirty water, soil, and pulp after provious floating washing tank, so as to ensure the water in the subsequent washing tank is clean thus improve the cleaning performance.
The speed of the dewatering machine is 2000rpm running smoothly and low noise.(picture)
E.Plastic squeezer dryer
It will be used in the raw material drying in the washing system. Effectively remove the water and keep the moisture within 5%. Will largely improve the quality of the next plastic pelletizing processing. (Squeezer Picture)
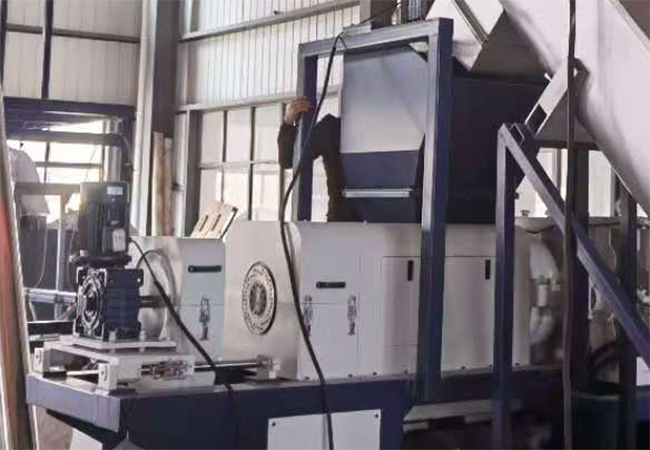
Models:
Model | NG300 | NG320 | NG350 |
Output(kg/h) | 500 | 700 | 1000 |
Raw material | PE films and yarn,PP films and yarn | PE films and yarn,PP films and yarn | PE films and yarn,PP films and yarn |
PP, PE film and PP woven bags recycling system china plastic washing machine production line is used to crush, wash, dewater and dry PP/PE film, PP woven bags which comes from post consumer or post industrial. The raw material can be the waste agriculture films, waste packing films etc.
Our plastic washing line features in the simple structure, easy operation, good performance, high capacity and low consumption etc. It will save much energy and labour.
After the raw materials washed well and dry well, it will get into the pelletizing line. The pelletizing line will process and pelletize the raw material to make it the nice plastic pellets for the next production. Either the material will be sold or to make the new films or bags.
A plastic recycling and granulating machine is a type of equipment used to recycle plastic waste into granules or pellets that can be reused in manufacturing new plastic products. The machine typically works by shredding or grinding the plastic waste into small pieces, then melting and extruding it through a die to form pellets or granules.
There are different types of plastic recycling and granulating machines available, including single-screw and twin-screw extruders. Some machines also include additional features such as screens to remove impurities from the plastic waste or cooling systems to ensure the pellets are solidified properly. PET bottle washing machine, PP woven bags washing line
Plastic recycling and granulating machines are commonly used in industries that generate large amounts of plastic waste, such as packaging, automotive, and construction. By recycling plastic waste, these machines help reduce the environmental impact of plastic disposal and conserve resources by reusing materials that would otherwise be discarded.